martes, 11 de octubre de 2011
martes, 6 de septiembre de 2011
Acciones Variables
Artículo 9.º Clasificación de acciones
Las acciones a considerar en el proyecto de una estructura o elemento estructural
se pueden clasificar según los criterios siguientes:
Clasificación por su naturaleza.
Clasificación por su variación en el tiempo.
9.1. Clasificación de las acciones por su naturaleza
Las acciones se pueden clasificar según su naturaleza en los siguientes grupos:
Acciones directas. Son aquellas que se aplican directamente sobre la estructura. En
este grupo se incluyen el peso propio de la estructura, las restantes cargas permanentes,
las sobrecargas de uso, etc.
Acciones indirectas. Son aquellas deformaciones o aceleraciones impuestas
capaces de dar lugar a esfuerzos. En este grupo se incluyen los efectos debidos a la
temperatura, asientos de la cimentación, desplazamientos impuestos, acciones sísmicas,
etc.
9.2. Clasificación de las acciones por su variación en el tiempo
Las acciones se pueden clasificar por su variación en el tiempo en los siguientes
grupos:
Acciones Permanentes (G). Son aquellas que actúan en todo momento y son
constantes en magnitud y posición. Dentro de este grupo se engloban el peso propio de
la estructura, de solados y pavimentos, de accesorios e instalaciones fijas, etc.
Acciones Permanentes de Valor no Constante (G
todo momento pero cuya magnitud no es constante y varía de forma monótona, como por
ejemplo, movimientos diferidos de la cimentación.
Acciones Variables (Q). Son aquellas cuyo valor varía frecuentemente a lo largo del
tiempo, de forma no monótona. Dentro de este grupo se incluyen sobrecargas de uso,
acciones climáticas, acciones debidas al proceso constructivo, etc.
*). Son aquellas que actúan enAcciones Accidentales (A). Son aquellas cuya probabilidad de actuación a lo largo
de la vida útil de la estructura es pequeña pero tienen una magnitud importante. En este
grupo se incluyen las acciones debidas a impactos, explosiones, etc. Los efectos
sísmicos pueden considerarse de este tipo.
La acción de incendio se entiende como situación accidental de proyecto y se
analiza en el Capítulo XII de esta Instrucción.
9.3. Clasificación de las acciones por su variación en el espacio
Las acciones se pueden clasificar según su variación en el espacio en los
siguientes grupos:
Acciones fijas. Son aquellas que se aplican siempre en la misma posición. Dentro
de este grupo se incluyen básicamente las acciones debidas al peso propio de los
elementos estructurales y funcionales.
Acciones libres. Son aquellas cuya posición puede ser variable en la estructura.
Dentro de este grupo se incluyen, por ejemplo, las sobrecargas de uso.
Artículo 10.º Valores característicos de las acciones
10.1. Generalidades
El valor característico de una acción es su valor de referencia a efectos de
proyecto. Puede venir determinado por un valor medio, un valor nominal o, en los casos
en que se fije mediante criterios estadísticos, por un valor correspondiente a una
determinada probabilidad de no ser superado durante un período de referencia, que tiene
en cuenta la vida útil de la estructura y la duración de la acción.
10.2. Valores característicos de las acciones permanentes
Para las acciones permanentes en las cuales se prevean dispersiones importantes,
o en aquellas que puedan tener una cierta variación durante el período de servicio de la
estructura, tales como balasto, pavimento, solados, se tomarán los valores característicos
superior e inferior. En caso contrario es suficiente adoptar un único valor.
En general, para el peso propio de la estructura se adoptará como valor
característico un único valor deducido de las dimensiones nominales y de los pesos
específicos nominales. Para los productos de acero se tomará el siguiente valor del peso
específico:
Acero: 78,5 kN/m
Artículo 11.º Valores representativos de las acciones
El valor representativo de una acción es el valor de la misma utilizado para la
comprobación de los estados límite.
Una misma acción puede tener uno o varios valores representativos, según sea su
tipo.
El valor representativo de una acción es su valor característico F
por un coeficiente
k o éste afectadoΨi de simultaneidad.Ψ
i FkComo valores característicos de las acciones se tomarán los indicados en las
Instrucciones o Normas de acciones vigentes.
Artículo 12.º Valores de cálculo de las acciones
Se define como valor de cálculo de una acción el obtenido como producto del valor
representativo (Artículo 11º) por un coeficiente parcial de seguridad.
Instrucción EAE. Capítulo III
29
F
d = γf Ψi Fkdonde:
F
d Valor de cálculo de la acción F.γ
12.1. Estados límite últimos
Como coeficientes parciales de seguridad de las acciones para las comprobaciones
de los estados límite últimos se adoptan los valores de la tabla 12.1, siempre que las
Instrucciones correspondientes de acciones no establezcan otros criterios.
Tabla 12.1
Coeficientes parciales de seguridad para las acciones, aplicables para la evaluación
de los estados límite últimos
TIPO DE ACCIÓN Situaciones persistentes o
transitorias
Situaciones accidentales
Efecto
favorable
Efecto
desfavorable
Efecto
favorable
Efecto
desfavorable
Permanente
Permanente de
valor no constante
Variable
Accidental - -
En general, para las acciones permanentes, la obtención de su efecto favorable o
desfavorable se determina ponderando todas las acciones del mismo origen con el
mismo coeficiente, indicado en la tabla 12.1.
Cuando los resultados de una comprobación sean muy sensibles a las variaciones
de la magnitud de la acción permanente, de una parte a otra de la estructura, las partes
favorable y desfavorable de dicha acción se considerarán como acciones individuales. En
particular, esto se aplica en la comprobación del estado límite de equilibrio en el que para
la parte favorable se adoptará un coeficiente
adoptará un coeficiente
favorable y
γG = 1,00 γG = 1,35 γG = 1,00 γG = 1,00γG* = 1,00 γG* = 1,50 γG* = 1,00 γG* = 1,00γQ = 0,00 γQ = 1,50 γQ = 0,00 γQ = 1,00γA = 1,00 γA = 1,00γG = 0,9 y para la parte desfavorable seγG = 1,1, para situaciones de servicio, ó γG = 0,95 para la parteγG = 1,05 para la parte desfavorable, para situaciones de construcción.12.2. Estados límite de servicio
Como coeficientes parciales de seguridad de las acciones para las comprobaciones
de los estados límite de servicio se adoptan los valores de la tabla 12.2.
Tabla 12.2
Coeficientes parciales de seguridad para las acciones, aplicables para la evaluación
de los estados límite de servicio
TIPO DE ACCIÓN Efecto favorable Efecto desfavorable
Permanente
Permanente de valor no constante
Variable
Artículo 13.º Combinación de acciones
13.1. Principios generales
Para cada una de las situaciones estudiadas se establecerán las posibles
combinaciones de acciones. Una combinación de acciones consiste en un conjunto de
acciones compatibles que se considerarán actuando simultáneamente para una
comprobación determinada.
Cada combinación, en general, estará formada por las acciones permanentes, una
acción variable determinante y una o varias acciones variables concomitantes. Cualquiera
de las acciones variables puede ser determinante.
13.2. Estados límite últimos
Para las distintas situaciones de proyecto, las combinaciones de acciones se
definirán de acuerdo con las siguientes expresiones:
En situaciones persistentes o transitorias:
Valor característico de las acciones permanentesconcomitantes con la acción variable determinante
Valor representativo de combinación de las acciones variables Valor representativo frecuente de la acción variable determinanteconcomitantes con la acción variable determinante y la acción accidental, o con la acción
sísmica
A
A
En las situaciones persistentes o transitorias, cuando la acción determinante
sea obvia, se valorarán distintas posibilidades considerando diferentes acciones variables
como determinantes.
En estructuras de edificación, simplificadamente, para las distintas situaciones de
proyecto, podrán considerarse las siguientes combinaciones:
Valor representativo cuasipermanente de las acciones variablesk Valor característico de la acción accidentalE,k Valor característico de la acción sísmicaQk,1 noEl estado límite último de fatiga, en el estado actual del conocimiento, supone
comprobaciones especiales que dependen de los elementos a dimensionar (elementos
estructurales, aceros de construcción, uniones, tornillos, etc.) y de los detalles
constructivos. El dimensionamiento y la comprobación frente a fatiga se harán de acuerdo
con lo recogido en el Capítulo XI de esta Instrucción.
13.3. Estados límite de servicio
Para estos estados límite se consideran únicamente las situaciones de proyecto
persistentes y transitorias. En estos casos, las combinaciones de acciones se definirán de
acuerdo con las siguientes expresiones:
Combinación poco probable
En estructuras de edificación, simplificadamente, para las distintas situaciones de
proyecto, podrán considerarse las siguientes combinaciones:
Combinación poco probable o frecuente
a) Combinación con una sola acción variable Q
k,1lunes, 5 de septiembre de 2011
tabla de elasticidad de diferentes materiales
Valor Modulo de Elasticidad aproximado (Kg/cm2)
Material
Mamposteria de ladrillo
E = 30000 - 50000
En Mexico, se puede calcular segun las NTC de mamposteria, de la siguiente manera:
Para mampostería de tabique de barro y otras piezas, excepto las de concreto:
Em = 600 fm* para cargas de corta duración
Em = 350 fm* para cargas sostenidas
fm* resistencia de diseño a compresión de la mampostería, referida al área bruta.
Maderas duras (en la dirección paralela a las fibras)
E = 100000 - 225000
Maderas blandas (en la dirección paralela a las fibras
E = 90000 - 110000
Acero
E = 2100000
Hierro de fundición
E = 1000000
Vidrio
E = 700000
Aluminio
E = 700000
Concreto (Hormigon) de Resistencia:
E =
110 Kg/cm2.
215000
130 Kg/cm2.
240000
170 Kg/cm2.
275000
300000
210 Kg/cm2.
340000
300 Kg/cm2.
370000
390000
Rocas:
E =
800000
Granito de grano grueso y en general
100000 - 400000
Cuarcita
100000 - 450000
Marmol
800000
Caliza en general
100000 - 800000
Dolomia
100000 - 710000
Arenisca en general
20000 - 636000
Arenisca calcárea
30000 - 60000
40000 - 200000
Gneis
100000 - 400000
Material
Mamposteria de ladrillo
E = 30000 - 50000
En Mexico, se puede calcular segun las NTC de mamposteria, de la siguiente manera:
Para mampostería de tabique de barro y otras piezas, excepto las de concreto:
Em = 600 fm* para cargas de corta duración
Em = 350 fm* para cargas sostenidas
fm* resistencia de diseño a compresión de la mampostería, referida al área bruta.
Maderas duras (en la dirección paralela a las fibras)
E = 100000 - 225000
Maderas blandas (en la dirección paralela a las fibras
E = 90000 - 110000
Acero
E = 2100000
Hierro de fundición
E = 1000000
Vidrio
E = 700000
Aluminio
E = 700000
Concreto (Hormigon) de Resistencia:
E =
110 Kg/cm2.
215000
130 Kg/cm2.
240000
170 Kg/cm2.
275000
300000
210 Kg/cm2.
340000
300 Kg/cm2.
370000
390000
Rocas:
E =
800000
Granito de grano grueso y en general
100000 - 400000
Cuarcita
100000 - 450000
Marmol
800000
Caliza en general
100000 - 800000
Dolomia
100000 - 710000
Arenisca en general
20000 - 636000
Arenisca calcárea
30000 - 60000
40000 - 200000
Gneis
100000 - 400000
Modulos de elasticidad del concreto y del acero

martes, 30 de agosto de 2011
losa reticular
Este tipo de losas se elabora a base de un sistema de entramado de trabes cruzadas que forman una retícula, dejando huecos intermedios que pueden ser ocupados permanentemente por bloques huecos o materiales cuyo peso volumétrico no exceda de 900kg/m y sean capaces de resistir una carga concentrada de una tonelada. La combinación de elementos prefabricados de concreto simple en forma de cajones con nervaduras de concreto reforzado colado en el lugar que forman una retícula que rodea por sus cuatro costados a los bloques prefabricados. También pueden colocarse, temporalmente a manera de cimbra para el colado de las trabes, casetones de plástico prefabricados que una vez fraguado el concreto deben retirarse y lavarse para usos posteriores. Con lo que resulta una losa liviana, de espesor uniforme.
Entre sus ventajas se encuentra
• Los esfuerzos de flexión y corte son relativamente bajos y repartidos en grandes areas.
• Permite colocar muros divisorios libremente.
• Se puede apoyar directamente sobre las columnas sin necesidad de trabes de carga entre columna y columna.
• Resiste fuertes cargas concentradas, ya que se distribuyen a areas muy grandes a través de las nervaduras cercanas de ambas direcciones.
• Las losas reticulares son más livianas y más rígidas que las losas macizas.
• El volumen de los colados en la obra es reducido.
• Mayor duración de la madera de cimbra, ya que sólo se adhiere a las nervaduras, y puede utilizarse más veces
• Este sistema reticular celulado da a las estructuras un aspecto agradable de ligereza y esbeltez.
• El entrepiso plano por ambas caras le da un aspecto mucho más limpio a la estructura y permite aprovechar la altura real que hay de piso a techo para el paso de luz natural. La superficie para acabados presenta características óptimas para que le yeso se adhiera perfectamente, dejando una superficie lisa, sin ocasionar grietas.
• Permite la modulación con claros cada vez mayores, lo que significa una reducción considerable en el número de columnas.
• La construcción de este tipo de losa proporciona un aislamiento acústico y térmico.
• La ausencia de trabes a la vista elimina el falso plafón.
• Permite la presencia de voladizos de las losas, que alcanzan sin problema 3 y 4 metros.
• Mayor rigidez de los entrepisos, gran estabilidad a las cargas dinámicas, soporta cargas muy fuertes.
• Su aplicación es muy variada y flexible, bien puede utilizarse en edificios de pocos niveles, ó grandes edificaciones, para construcciones de índole público, escuelas, centros comerciales, hospitales, oficinas, multifamiliares, bodegas, almacenes, construcciones industriales ó casas económicas en serie o residencias particulares.
Los cajones prefabricados se colocan sobre una cimbra plana, dispuestos por pares, uno de fondo y otro de tapa que forman una celda interior cerrada, en el espacio que queda entre los bloques se coloca el refuerzo y se cuela el concreto de las nervaduras. Los cajones y las nervaduras pasan a formar nervaduras de sección doble T, que son elementos resistentes del entrepiso reticular celulado. Para que las secciones doble T sean estructuralmente correctas, debe admitirse un monolitismo absoluto entre los elementos prefabricas y el concreto colado en el lugar.
Los bloques precolados se fabrican en tres peraltes diferentes: 20, 17.5 y 12.5centímetros. En planta las dimensiones standard son: 85 x 85cm, 85 x 75cm y 65 x 65cm. Combinando varias medidas de bloques haciendo variar ligeramente el ancho de las nervaduras, se puede cubrir cualquier claro. El concreto utilizado en la fabricación es de una resistencia mínima de 140kg/cm a los 28 días. El espesor promedio de la pared del bloque es de 1.5cm y el fondo de 1.5 a 3 cm.

Procedimiento constructivo
Cimbra
Deberá estar perfectamente al nivel requerido, será plana, cuidada y resistente de madera o de metal.
Trazo de la retícula.
Se trazan sobre la cimbra los espacios que corresponden a las hileras de bloques de borde, las hileras interiores de cajones formados por los bloques se localizará fácilmente mediante reventones, tomados desde los elementos extremos, conviene indicar sobre la cimbra la posición de estos bloques, con trazos no necesariamente continuos.
Colocación de los bloques. Se podrá hacer al mismo tiempo que el trazo de la retícula, el manejo y colocación de los bloques se hace fácilmente a mano, procurando que asienten muy bien sobre la cimbra.
Armado
Para obtener un recubrimiento adecuado en el refuerzo metálico, conviene colocar calzas, una por cada bloque, sobre las cuales se tienden las varillas del refuerzo inferior, primero en un sentido y luego en otro. A continuación se ponen los estribos en ambas direcciones, después se coloca el refuerzo superior, amarrándose con los estribos, en la posición indicada en los planos constructivos. En la zona del capitel debe revisarse cuidadosamente la colocación del refuerzo, pues es la zona sometida a los máximos esfuerzos y la colocación de su armado es a base de varillas rectas, en las nervaduras del capitel que van de columna a columna y las dos laterales, se colocan dos varillas abajo y dos arriba, aumentando en el capitel la cantidad necesaria para tomar los esfuerzos. En las nervaduras centrales del claro se dispone sólo de una varilla inferior y otra superior. Todo armado dispone sólo de una varilla inferior y otra superior. Todo armado dependerá principalmente del diseño y del cálculo.
Para introducir las instalaciones eléctricas, se colocan sobre el bloque donde se requiera la instalación y se perfora, estás tuberías o ductos deberán colocarse después de tener terminado todo el armado.
Para las instalaciones sanitarias que generalmente están concentradas en zonas definidas es conveniente alojarlas en esa zona o se puede colgar dichas tuberías de la estructura, pero se tendrá que utilizar un falso plafón Colado.
En las nervaduras centrales, que son las más angostas se debera tener controlado el colado para asegurarse de que se llene el reducido ancho de la nervadura y una vez que el concreto llegue al nivel de los bloques se enrasará al nivel requerido.
Para colados interrumpidos deberán dejarse las juntas en los sitios de menor esfuerzo.
Descimbrar.
Es fácil y rápido, porque la cimbra se adhiere solamente al concreto de las nervaduras, conservándose mucho mejor y teniendo mayor duración.
Acabados.
Se puede enyesar o aplanar directamente la cara inferior de la losa, ya que la superficie del bloque y de las nervaduras tienen una excelente adherencia a estos acabados. En la cara superior bastará con colocar un fino muy delgado para terminar la superficie y colocar el piso final, o bien entortado para colocar un acabado pétreo. En las losas de azotea la impermeabilización se hace como en cualquier losa de cubierta en azoteas.
Entre sus ventajas se encuentra
• Los esfuerzos de flexión y corte son relativamente bajos y repartidos en grandes areas.
• Permite colocar muros divisorios libremente.
• Se puede apoyar directamente sobre las columnas sin necesidad de trabes de carga entre columna y columna.
• Resiste fuertes cargas concentradas, ya que se distribuyen a areas muy grandes a través de las nervaduras cercanas de ambas direcciones.
• Las losas reticulares son más livianas y más rígidas que las losas macizas.
• El volumen de los colados en la obra es reducido.
• Mayor duración de la madera de cimbra, ya que sólo se adhiere a las nervaduras, y puede utilizarse más veces
• Este sistema reticular celulado da a las estructuras un aspecto agradable de ligereza y esbeltez.
• El entrepiso plano por ambas caras le da un aspecto mucho más limpio a la estructura y permite aprovechar la altura real que hay de piso a techo para el paso de luz natural. La superficie para acabados presenta características óptimas para que le yeso se adhiera perfectamente, dejando una superficie lisa, sin ocasionar grietas.
• Permite la modulación con claros cada vez mayores, lo que significa una reducción considerable en el número de columnas.
• La construcción de este tipo de losa proporciona un aislamiento acústico y térmico.
• La ausencia de trabes a la vista elimina el falso plafón.
• Permite la presencia de voladizos de las losas, que alcanzan sin problema 3 y 4 metros.
• Mayor rigidez de los entrepisos, gran estabilidad a las cargas dinámicas, soporta cargas muy fuertes.
• Su aplicación es muy variada y flexible, bien puede utilizarse en edificios de pocos niveles, ó grandes edificaciones, para construcciones de índole público, escuelas, centros comerciales, hospitales, oficinas, multifamiliares, bodegas, almacenes, construcciones industriales ó casas económicas en serie o residencias particulares.
Los cajones prefabricados se colocan sobre una cimbra plana, dispuestos por pares, uno de fondo y otro de tapa que forman una celda interior cerrada, en el espacio que queda entre los bloques se coloca el refuerzo y se cuela el concreto de las nervaduras. Los cajones y las nervaduras pasan a formar nervaduras de sección doble T, que son elementos resistentes del entrepiso reticular celulado. Para que las secciones doble T sean estructuralmente correctas, debe admitirse un monolitismo absoluto entre los elementos prefabricas y el concreto colado en el lugar.
Los bloques precolados se fabrican en tres peraltes diferentes: 20, 17.5 y 12.5centímetros. En planta las dimensiones standard son: 85 x 85cm, 85 x 75cm y 65 x 65cm. Combinando varias medidas de bloques haciendo variar ligeramente el ancho de las nervaduras, se puede cubrir cualquier claro. El concreto utilizado en la fabricación es de una resistencia mínima de 140kg/cm a los 28 días. El espesor promedio de la pared del bloque es de 1.5cm y el fondo de 1.5 a 3 cm.

Procedimiento constructivo
Cimbra
Deberá estar perfectamente al nivel requerido, será plana, cuidada y resistente de madera o de metal.
Trazo de la retícula.
Se trazan sobre la cimbra los espacios que corresponden a las hileras de bloques de borde, las hileras interiores de cajones formados por los bloques se localizará fácilmente mediante reventones, tomados desde los elementos extremos, conviene indicar sobre la cimbra la posición de estos bloques, con trazos no necesariamente continuos.
Colocación de los bloques. Se podrá hacer al mismo tiempo que el trazo de la retícula, el manejo y colocación de los bloques se hace fácilmente a mano, procurando que asienten muy bien sobre la cimbra.
Armado
Para obtener un recubrimiento adecuado en el refuerzo metálico, conviene colocar calzas, una por cada bloque, sobre las cuales se tienden las varillas del refuerzo inferior, primero en un sentido y luego en otro. A continuación se ponen los estribos en ambas direcciones, después se coloca el refuerzo superior, amarrándose con los estribos, en la posición indicada en los planos constructivos. En la zona del capitel debe revisarse cuidadosamente la colocación del refuerzo, pues es la zona sometida a los máximos esfuerzos y la colocación de su armado es a base de varillas rectas, en las nervaduras del capitel que van de columna a columna y las dos laterales, se colocan dos varillas abajo y dos arriba, aumentando en el capitel la cantidad necesaria para tomar los esfuerzos. En las nervaduras centrales del claro se dispone sólo de una varilla inferior y otra superior. Todo armado dispone sólo de una varilla inferior y otra superior. Todo armado dependerá principalmente del diseño y del cálculo.
Para introducir las instalaciones eléctricas, se colocan sobre el bloque donde se requiera la instalación y se perfora, estás tuberías o ductos deberán colocarse después de tener terminado todo el armado.
Para las instalaciones sanitarias que generalmente están concentradas en zonas definidas es conveniente alojarlas en esa zona o se puede colgar dichas tuberías de la estructura, pero se tendrá que utilizar un falso plafón Colado.
En las nervaduras centrales, que son las más angostas se debera tener controlado el colado para asegurarse de que se llene el reducido ancho de la nervadura y una vez que el concreto llegue al nivel de los bloques se enrasará al nivel requerido.
Para colados interrumpidos deberán dejarse las juntas en los sitios de menor esfuerzo.
Descimbrar.
Es fácil y rápido, porque la cimbra se adhiere solamente al concreto de las nervaduras, conservándose mucho mejor y teniendo mayor duración.
Acabados.
Se puede enyesar o aplanar directamente la cara inferior de la losa, ya que la superficie del bloque y de las nervaduras tienen una excelente adherencia a estos acabados. En la cara superior bastará con colocar un fino muy delgado para terminar la superficie y colocar el piso final, o bien entortado para colocar un acabado pétreo. En las losas de azotea la impermeabilización se hace como en cualquier losa de cubierta en azoteas.
lunes, 29 de agosto de 2011
Cortante, Momento y Torcion
Cortante
El esfuerzo cortante, de corte, de cizalla o de cortadura es el esfuerzo interno o resultante de las tensiones paralelas a la sección transversal de un prisma mecánico como por ejemplo una viga o un pilar. Se designa variadamente como T, V o Q
Este tipo de solicitación formado por tensiones paralelas está directamente asociado a la tensión cortante Para una pieza prismática se relaciona con la tensión cortante mediante la relación.
En mecánica newtoniana, se denomina momento de una fuerza (respecto a un punto dado) a una magnitud vectorial, obtenida como producto vectorial del vector de posición del punto de aplicación de la fuerza con respecto al punto al cual se toma el momento por la fuerza, en ese orden. También se le denomina momento dinámico o sencillamente momento.
Ocasionalmente recibe el nombre de torque a partir del término inglés (torque), derivado a su vez del latín torquere (retorcer). Este término intenta introducirse en la terminología española, bajo las formas de torque o torca, aunque con escasa fortuna, ya que existe la denominación par que es la correcta en español.
El momento angular o momento cinético es una magnitud física importante en todas las teorías físicas de la mecánica, desde la mecánica clásica a la mecánica cuántica, pasando por la mecánica relativista. Su importancia en todas ellas se debe a que está relacionada con las simetrías rotacionales de los sistemas físicos. Bajo ciertas condiciones de simetría rotacional de los sistemas es una magnitud que se mantiene constante con el tiempo a medida que el sistema evoluciona, lo cual da lugar a una ley de conservación conocida como ley de conservación del momento angular. El momento angular para un cuerpo rígido que rota respecto a un eje, es la resistencia que ofrece dicho cuerpo a la variación de la velocidad angular. En el Sistema Internacional de Unidades el momento angular se mide en kg·m²/s.
Esta magnitud desempeña respecto a las rotaciones un papel análogo al momento lineal en las traslaciones. Sin embargo, eso no implica que sea una magnitud exclusiva de las rotaciones; por ejemplo, el momento angular de una partícula que se mueve libremente con velocidad constante (en módulo y dirección) también se conserva.
El nombre tradicional en español es momento cinético,pero por influencia del inglés angular momentum hoy son frecuentes momento angular y otras variantes como cantidad de movimiento angular o ímpetu angular
Torsion
En ingeniería, torsión es la solicitación que se presenta cuando se aplica un momento sobre el eje longitudinal de un elemento constructivo o prisma mecánico, como pueden ser ejes o, en general, elementos donde una dimensión predomina sobre las otras dos, aunque es posible encontrarla en situaciones diversas.
La torsión se caracteriza geométricamente porque cualquier curva paralela al eje de la pieza deja de estar contenida en el plano formado inicialmente por las dos curvas. En lugar de eso una curva paralela al eje se retuerce alrededor de él (ver torsión geométrica).
El estudio general de la torsión es complicado porque bajo ese tipo de solicitación la sección transversal de una pieza en general se caracteriza por dos fenómenos:
El esfuerzo cortante, de corte, de cizalla o de cortadura es el esfuerzo interno o resultante de las tensiones paralelas a la sección transversal de un prisma mecánico como por ejemplo una viga o un pilar. Se designa variadamente como T, V o Q
Este tipo de solicitación formado por tensiones paralelas está directamente asociado a la tensión cortante Para una pieza prismática se relaciona con la tensión cortante mediante la relación.
Momento
En mecánica newtoniana, se denomina momento de una fuerza (respecto a un punto dado) a una magnitud vectorial, obtenida como producto vectorial del vector de posición del punto de aplicación de la fuerza con respecto al punto al cual se toma el momento por la fuerza, en ese orden. También se le denomina momento dinámico o sencillamente momento.
Ocasionalmente recibe el nombre de torque a partir del término inglés (torque), derivado a su vez del latín torquere (retorcer). Este término intenta introducirse en la terminología española, bajo las formas de torque o torca, aunque con escasa fortuna, ya que existe la denominación par que es la correcta en español.
Momento angular
El momento angular o momento cinético es una magnitud física importante en todas las teorías físicas de la mecánica, desde la mecánica clásica a la mecánica cuántica, pasando por la mecánica relativista. Su importancia en todas ellas se debe a que está relacionada con las simetrías rotacionales de los sistemas físicos. Bajo ciertas condiciones de simetría rotacional de los sistemas es una magnitud que se mantiene constante con el tiempo a medida que el sistema evoluciona, lo cual da lugar a una ley de conservación conocida como ley de conservación del momento angular. El momento angular para un cuerpo rígido que rota respecto a un eje, es la resistencia que ofrece dicho cuerpo a la variación de la velocidad angular. En el Sistema Internacional de Unidades el momento angular se mide en kg·m²/s.
Esta magnitud desempeña respecto a las rotaciones un papel análogo al momento lineal en las traslaciones. Sin embargo, eso no implica que sea una magnitud exclusiva de las rotaciones; por ejemplo, el momento angular de una partícula que se mueve libremente con velocidad constante (en módulo y dirección) también se conserva.
El nombre tradicional en español es momento cinético,pero por influencia del inglés angular momentum hoy son frecuentes momento angular y otras variantes como cantidad de movimiento angular o ímpetu angular
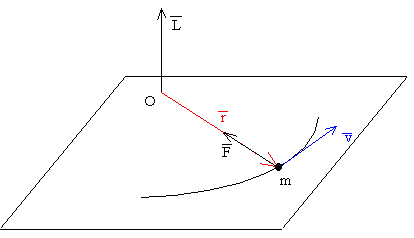
En ingeniería, torsión es la solicitación que se presenta cuando se aplica un momento sobre el eje longitudinal de un elemento constructivo o prisma mecánico, como pueden ser ejes o, en general, elementos donde una dimensión predomina sobre las otras dos, aunque es posible encontrarla en situaciones diversas.
La torsión se caracteriza geométricamente porque cualquier curva paralela al eje de la pieza deja de estar contenida en el plano formado inicialmente por las dos curvas. En lugar de eso una curva paralela al eje se retuerce alrededor de él (ver torsión geométrica).
El estudio general de la torsión es complicado porque bajo ese tipo de solicitación la sección transversal de una pieza en general se caracteriza por dos fenómenos:
- Aparecen tensiones tangenciales paralelas a la sección transversal. Si estas se representan por un campo vectorial sus líneas de flujo "circulan" alrededor de la sección.
- Cuando las tensiones anteriores no están distribuidas adecuadamente, cosa que sucede siempre a menos que la sección tenga simetría circular, aparecen alabeos seccionales que hacen que las secciones transversales deformadas no sean planas.
miércoles, 24 de agosto de 2011
Varillas
Las varillas se utilizan como refuerzo de concreto; son barras de acero generalmente de sección circular con diámetro superior a los 5 milímetros, aunque por lo común sus diámetros se especifican en fracciones de pulgada.
La superficie de estos cilindros está provista de rebordes (corrugaciones) que mejoran la adherencia a los materiales aglomerantes e inhiben el movimiento relativo longitudinal entre la varilla y el concreto que la rodea, y de hecho el papel de las varillas no es sólo reforzar la estructura del concreto armado, sino absorber los esfuerzos de tracción y torsión.
Se fabrican varillas de sección redonda, que pueden ser lisas o estradas, y también de sección cuadrada, más empleadas en herrería.

lunes, 22 de agosto de 2011
Elaboracion de concreto en obra
Ingredientes del concreto
El concreto fresco es una mezcla semilíquida de cemento portland, arena (agregado fino), grava o piedra triturada (agregado grueso) yagua. Mediante un proceso llamado hidratación, las partículas del cemento reaccionan químicamente con el agua y el concreto se endurece y se convierte en un material durable. Cuando se mezcla, se hace el vaciado y se cura de manera apropiada, el concreto forma estructuras sólidas capaces de soportar las temperaturas extremas del invierno y del verano sin requerir de mucho mantenimiento. El material que se utilice en la preparación del concreto afecta la facilidad con que pueda vaciarse y con la que se le pueda dar el acabado; también influye en el tiempo que tarde en endurecer, la resistencia que pueda adquirir, y lo bien que cumpla las funciones para las que fue preparado.
Además de los ingredientes de la mezcla de concreto en sí misma, será necesario un marco o cimbra y un refuerzo de acero para construir estructuras sólidas. La cimbra generalmente se construye de madera y puede hacerse con ella desde un sencillo cuadrado hasta formas más complejas, dependiendo de la naturaleza del proyecto. El acero reforzado puede ser de alta o baja resistencia, características que dependerán de las dimensiones y la resistencia que se requieran. El concreto se vacía en la cimbra con la forma deseada y después la superficie se alisa y se le da el acabado con diversas texturas.
AGUA PARA CONCRETO
USOS DEL AGUA
En relación con su empleo en el concreto, el agua tiene dos diferentes aplicaciones: como ingrediente en la elaboración de las mezclas y como medio fe curado de las estructuras recién construidas. En el primer caso es de lS0 interno como agua de mezclado, y en el segundo se emplea exteriormente =cuando el concreto se cura con agua. aunque en estas aplicaciones las características del agua tienen efectos de diferente importancia sobre el concreto, es usual que se recomiende emplear igual de una sola calidad en ambos casos. Así, normalmente, en las especificaciones para concreto se hace referencia en primer término a los requisitos que debe cumplir el agua para elaborar el concreto, porque sus efectos son más importantes, y después se indica que el agua que se utilice para curarlo debe ser del mismo origen, o similar, para evitar que se subestime esta segunda aplicación y se emplee agua de curado con características inadecuadas.
En determinados casos se requiere, con objeto de disminuir la temperatura del concreto al ser elaborado, que una parte del agua de mezclado se administre en forma de hielo molido o en escamas. En tales casos, el agua que se utilice para fabricar el hielo debe satisfacer las mismas especificaciones de calidad del agua de mezclado.
Como componente del concreto convencional, el agua suele representar aproximadamente entre lO y 25 por ciento del volumen del concreto recién mezclado, dependiendo del tamaño máximo de agregado que se utilice y del revenimiento que se requiera(38). Esto le concede una influencia importante a la calidad del agua de mezclado en el comportamiento y las propiedades del concreto, pues cualquier substancia dañina que contenga, aún en proporciones reducidas, puede tener efectos adversos significativos en el concreto.
El concreto fresco es una mezcla semilíquida de cemento portland, arena (agregado fino), grava o piedra triturada (agregado grueso) yagua. Mediante un proceso llamado hidratación, las partículas del cemento reaccionan químicamente con el agua y el concreto se endurece y se convierte en un material durable. Cuando se mezcla, se hace el vaciado y se cura de manera apropiada, el concreto forma estructuras sólidas capaces de soportar las temperaturas extremas del invierno y del verano sin requerir de mucho mantenimiento. El material que se utilice en la preparación del concreto afecta la facilidad con que pueda vaciarse y con la que se le pueda dar el acabado; también influye en el tiempo que tarde en endurecer, la resistencia que pueda adquirir, y lo bien que cumpla las funciones para las que fue preparado.
Además de los ingredientes de la mezcla de concreto en sí misma, será necesario un marco o cimbra y un refuerzo de acero para construir estructuras sólidas. La cimbra generalmente se construye de madera y puede hacerse con ella desde un sencillo cuadrado hasta formas más complejas, dependiendo de la naturaleza del proyecto. El acero reforzado puede ser de alta o baja resistencia, características que dependerán de las dimensiones y la resistencia que se requieran. El concreto se vacía en la cimbra con la forma deseada y después la superficie se alisa y se le da el acabado con diversas texturas.
USOS DEL AGUA
En relación con su empleo en el concreto, el agua tiene dos diferentes aplicaciones: como ingrediente en la elaboración de las mezclas y como medio fe curado de las estructuras recién construidas. En el primer caso es de lS0 interno como agua de mezclado, y en el segundo se emplea exteriormente =cuando el concreto se cura con agua. aunque en estas aplicaciones las características del agua tienen efectos de diferente importancia sobre el concreto, es usual que se recomiende emplear igual de una sola calidad en ambos casos. Así, normalmente, en las especificaciones para concreto se hace referencia en primer término a los requisitos que debe cumplir el agua para elaborar el concreto, porque sus efectos son más importantes, y después se indica que el agua que se utilice para curarlo debe ser del mismo origen, o similar, para evitar que se subestime esta segunda aplicación y se emplee agua de curado con características inadecuadas.
En determinados casos se requiere, con objeto de disminuir la temperatura del concreto al ser elaborado, que una parte del agua de mezclado se administre en forma de hielo molido o en escamas. En tales casos, el agua que se utilice para fabricar el hielo debe satisfacer las mismas especificaciones de calidad del agua de mezclado.
Como componente del concreto convencional, el agua suele representar aproximadamente entre lO y 25 por ciento del volumen del concreto recién mezclado, dependiendo del tamaño máximo de agregado que se utilice y del revenimiento que se requiera(38). Esto le concede una influencia importante a la calidad del agua de mezclado en el comportamiento y las propiedades del concreto, pues cualquier substancia dañina que contenga, aún en proporciones reducidas, puede tener efectos adversos significativos en el concreto.
Concreto en planta
CONCRETO EN PLANTA
Planta de concreto es una instalación utilizada para la fabricación del concreto a partir de la materia prima que lo compone: agregados, cemento y agua (también puede incluir otros componentes como filler, fibras de refuerzo o aditivos). Estos componentes que previamente se encuentran almacenados en la planta de concreto, son dosificados en las proporciones adecuadas, para ser mezclados en el caso de centrales mezcladoras o directamente descargados a un camión concretera en el caso de las centrales dosificadoras
Tipos de plantas de concreto
La planta de concreto se puede clasificar desde varios puntos de vista:

Tipos de plantas de concreto
La planta de concreto se puede clasificar desde varios puntos de vista:
Según el tipo de concreto que se produce.
-Plantas de mezclado: para la producción de concreto premezclado, Incluyen una mezcladora, que es la encargada de homogeneizar la masa de concreto.
-Plantas de dosificado: para la producción de concreto dosificado, a veces llamado concreto seco. La principal característica de estas plantas, es que carecen de mezcladora. La mezcla de componentes dosificados, se vierte en un camión concretera que es el encargado de homogeneizar la mezcla.
-Plantas de grava cemento: para la producción de una mezcla semi-seca de grava con cemento. Normalmente este tipo plantas realizan la dosificación y pesaje de los componentes en modo continuo.
-Plantas combinadas: para la producción de concreto premezclado y dosificado en una misma planta, mediante la utilización de un sistema de by-passes, que hacen que el concreto pase por la mezcladora o directamente se descargue en el camión concretera. El fabricante español Talleres Alquezar ( [1] ) lanzó al mercado la serie GMGC-DHA, para la producción con una sola instalación de concreto premezclado, dosificado y grava-cemento.
Según la movilidad de la planta.
-Plantas fijas: son las instalaciones destinadas a un centro productivo con una localización fija. La estructura de la planta se diseña e instala de con la idea de no ser trasladada a lo largo de la vida útil de la instalación.
-Plantas móviles: son las instalaciones destinadas a trabajar en una obra o proyecto concreto. Tras la finalización del mismo, la planta es desmontada, trasladada y ensamblada en otro lugar de trabajo. La estructura de la planta, suele incorporar un tren de rodadura, de manera que se necesita solamente una cabeza tractora para realizar el transporte de las principales partes de la planta.
-Plantas modulares: aquellas instalaciones destinadas a trabajar en varias localizaciones diferentes a lo largo de su vida útil, al igual que las plantas modulares. En este caso, la planta no se fabrica con sistema de rodadura, sino que se diseña en diferentes módulos estructurales, facilmente transportables mediante medios estandarizados (plataformas, contenedores, flat-racks...) El montaje de los diferentes módulos es rápido, ya que todos los elementos de la instalación están previamente preinstalados dentro de cada módulo.
Según el sistema de acopio de agragados
Según el lugar donde se almacenan los agregados que serán utilizados en el proceso de fabricación, tenemos dos tipos de plantas:
-Plantas verticales. En este tipo de plantas, el acopio de agragados se realiza en la parte superior de la planta, de manera que debe hacerse una elevación de los mismos previa al almacenamiento. La ventaja de este sistema es que los agragados se encuentran justo por encima del nivel de mezclado/dosificado, de manera que la descarga de los mismos en el momento justo en que se demandan es muy rápida, obteniendo de esta manera grandes producciones y buenos rendimientos sobre la capacidad máxima teórica de la mezcladora (en el caso de producción de concreto premezclado)

Planta de concreto es una instalación utilizada para la fabricación del concreto a partir de la materia prima que lo compone: agregados, cemento y agua (también puede incluir otros componentes como filler, fibras de refuerzo o aditivos). Estos componentes que previamente se encuentran almacenados en la planta de concreto, son dosificados en las proporciones adecuadas, para ser mezclados en el caso de centrales mezcladoras o directamente descargados a un camión concretera en el caso de las centrales dosificadoras
Tipos de plantas de concreto
La planta de concreto se puede clasificar desde varios puntos de vista:

Tipos de plantas de concreto
La planta de concreto se puede clasificar desde varios puntos de vista:
Según el tipo de concreto que se produce.
-Plantas de mezclado: para la producción de concreto premezclado, Incluyen una mezcladora, que es la encargada de homogeneizar la masa de concreto.
-Plantas de dosificado: para la producción de concreto dosificado, a veces llamado concreto seco. La principal característica de estas plantas, es que carecen de mezcladora. La mezcla de componentes dosificados, se vierte en un camión concretera que es el encargado de homogeneizar la mezcla.
-Plantas de grava cemento: para la producción de una mezcla semi-seca de grava con cemento. Normalmente este tipo plantas realizan la dosificación y pesaje de los componentes en modo continuo.
-Plantas combinadas: para la producción de concreto premezclado y dosificado en una misma planta, mediante la utilización de un sistema de by-passes, que hacen que el concreto pase por la mezcladora o directamente se descargue en el camión concretera. El fabricante español Talleres Alquezar ( [1] ) lanzó al mercado la serie GMGC-DHA, para la producción con una sola instalación de concreto premezclado, dosificado y grava-cemento.
Según la movilidad de la planta.
-Plantas fijas: son las instalaciones destinadas a un centro productivo con una localización fija. La estructura de la planta se diseña e instala de con la idea de no ser trasladada a lo largo de la vida útil de la instalación.
-Plantas móviles: son las instalaciones destinadas a trabajar en una obra o proyecto concreto. Tras la finalización del mismo, la planta es desmontada, trasladada y ensamblada en otro lugar de trabajo. La estructura de la planta, suele incorporar un tren de rodadura, de manera que se necesita solamente una cabeza tractora para realizar el transporte de las principales partes de la planta.
-Plantas modulares: aquellas instalaciones destinadas a trabajar en varias localizaciones diferentes a lo largo de su vida útil, al igual que las plantas modulares. En este caso, la planta no se fabrica con sistema de rodadura, sino que se diseña en diferentes módulos estructurales, facilmente transportables mediante medios estandarizados (plataformas, contenedores, flat-racks...) El montaje de los diferentes módulos es rápido, ya que todos los elementos de la instalación están previamente preinstalados dentro de cada módulo.
Según el sistema de acopio de agragados
Según el lugar donde se almacenan los agregados que serán utilizados en el proceso de fabricación, tenemos dos tipos de plantas:
-Plantas verticales. En este tipo de plantas, el acopio de agragados se realiza en la parte superior de la planta, de manera que debe hacerse una elevación de los mismos previa al almacenamiento. La ventaja de este sistema es que los agragados se encuentran justo por encima del nivel de mezclado/dosificado, de manera que la descarga de los mismos en el momento justo en que se demandan es muy rápida, obteniendo de esta manera grandes producciones y buenos rendimientos sobre la capacidad máxima teórica de la mezcladora (en el caso de producción de concreto premezclado)

Resistencia del concreto
La resistencia a la compresión se puede definir como la máxima resistencia medida de un espécimen de concreto o de mortero a carga axial. Generalmente se expresa en kilogramos por centímetro cuadrado (Kg/cm2) a una edad de 28 días se le designe con el símbolo f’ c. Para de terminar la resistencia a la compresión, se realizan pruebas especimenes de mortero o de concreto;
en los Estados Unidos, a menos de que se especifique de otra manera, los ensayes a compresión de mortero se realizan sobre cubos de 5 cm. en tanto que los ensayes a compresión del concreto se efectúan sobre cilindros que miden 15 cm de diámetro y 30 cm de altura. La resistencia del concreto a la compresión es una propiedad física fundamental, y es frecuentemente empleada el los cálculos para diseño de puente, de edificios y otras estructuras. El concreto de uso generalizado tiene una resistencia a la compresión entre 210 y 350 kg/cm cuadrado. un concreto de alta resistencia tiene una resistencia a la compresión de cuando menos 420 kg/cm cuadrado. resistencia de 1,400 kg/cm cuadrado se ha llegado a utilizar en aplicaciones de construcción . La resistencia a la flexión del concreto se utiliza generalmente al diseñar pavimentos y otras losas sobre el terreno. La resistencia a la compresión se puede utilizar como índice de la resistencia a la flexión, una ves que entre ellas se ha establecido la relación empírica para los materiales y el tamaño del elemento en cuestión. La resistencia a la flexión, también llamada modulo de ruptura, para un concreto de peso normal se aproxima a menudo de1.99 a 2.65 veces el valor de la raíz cuadrada de la resistencia a la compresión.
El valor de la resistencia a la tensión del concreto es aproximadamente de 8% a 12% de su resistencia a compresión y a menudo se estima como 1.33 a 1.99 veces la raíz cuadrada de la resistencia a compresión. La resistencia a la torsión para el concreto esta relacionada con el modulo de ruptura y con las dimensiones del elemento de concreto. La resistencia al cortante del concreto puede variar desde el 35% al 80% de la resistencia a compresión. La correlación existe entre la resistencia a la compresión y resistencia a flexión, tensión, torsión, y cortante, de acuerdo a los componentes del concreto y al medio ambiente en que se encuentre. El modulo de elasticidad, denotando por medio del símbolo E, se puedes definir como la relación del esfuerzo normal la deformación correspondiente para esfuerzos de tensión o de compresión por debajo del limite de proporcionalidad de un material. Para concretos de peso normal, E fluctúa entre 140,600 y 422,000 kg/cm cuadrado, y se puede aproximar como 15,100 veces el valor de la raíz cuadrada de la resistencia a compresión. Los principales factores que afectan a la resistencia son la relación Agua – Cemento y la edad, o el grado a que haya progresado la hidratación. Estos factores también afectan a la resistencia a flexión y a tensión, así como a la adherencia del concreto con el acero. Las relaciones Edad – Resistencia a compresión. Cuando se requiera de valores mas precisos para el concreto se deberán desarrollar curvas para los materiales específicos y para las proporciones de mezclado que se utilicen en el trabajo. Para una trabajabilidad y una cantidad de cemento dadas, el concreto con aire incluido necesita menos agua de mezclado que el concreto sin aire incluido. La menor relación Agua – Cemento que es posible lograr en un concreto con aire incluido tiende a compensar las resistencias mínimas inferiores del concreto con aire incluido, particularmente en mezclas con contenidos de cemento pobres e intermedios.
en los Estados Unidos, a menos de que se especifique de otra manera, los ensayes a compresión de mortero se realizan sobre cubos de 5 cm. en tanto que los ensayes a compresión del concreto se efectúan sobre cilindros que miden 15 cm de diámetro y 30 cm de altura. La resistencia del concreto a la compresión es una propiedad física fundamental, y es frecuentemente empleada el los cálculos para diseño de puente, de edificios y otras estructuras. El concreto de uso generalizado tiene una resistencia a la compresión entre 210 y 350 kg/cm cuadrado. un concreto de alta resistencia tiene una resistencia a la compresión de cuando menos 420 kg/cm cuadrado. resistencia de 1,400 kg/cm cuadrado se ha llegado a utilizar en aplicaciones de construcción . La resistencia a la flexión del concreto se utiliza generalmente al diseñar pavimentos y otras losas sobre el terreno. La resistencia a la compresión se puede utilizar como índice de la resistencia a la flexión, una ves que entre ellas se ha establecido la relación empírica para los materiales y el tamaño del elemento en cuestión. La resistencia a la flexión, también llamada modulo de ruptura, para un concreto de peso normal se aproxima a menudo de1.99 a 2.65 veces el valor de la raíz cuadrada de la resistencia a la compresión.
El valor de la resistencia a la tensión del concreto es aproximadamente de 8% a 12% de su resistencia a compresión y a menudo se estima como 1.33 a 1.99 veces la raíz cuadrada de la resistencia a compresión. La resistencia a la torsión para el concreto esta relacionada con el modulo de ruptura y con las dimensiones del elemento de concreto. La resistencia al cortante del concreto puede variar desde el 35% al 80% de la resistencia a compresión. La correlación existe entre la resistencia a la compresión y resistencia a flexión, tensión, torsión, y cortante, de acuerdo a los componentes del concreto y al medio ambiente en que se encuentre. El modulo de elasticidad, denotando por medio del símbolo E, se puedes definir como la relación del esfuerzo normal la deformación correspondiente para esfuerzos de tensión o de compresión por debajo del limite de proporcionalidad de un material. Para concretos de peso normal, E fluctúa entre 140,600 y 422,000 kg/cm cuadrado, y se puede aproximar como 15,100 veces el valor de la raíz cuadrada de la resistencia a compresión. Los principales factores que afectan a la resistencia son la relación Agua – Cemento y la edad, o el grado a que haya progresado la hidratación. Estos factores también afectan a la resistencia a flexión y a tensión, así como a la adherencia del concreto con el acero. Las relaciones Edad – Resistencia a compresión. Cuando se requiera de valores mas precisos para el concreto se deberán desarrollar curvas para los materiales específicos y para las proporciones de mezclado que se utilicen en el trabajo. Para una trabajabilidad y una cantidad de cemento dadas, el concreto con aire incluido necesita menos agua de mezclado que el concreto sin aire incluido. La menor relación Agua – Cemento que es posible lograr en un concreto con aire incluido tiende a compensar las resistencias mínimas inferiores del concreto con aire incluido, particularmente en mezclas con contenidos de cemento pobres e intermedios.
Cemento Portland
El cemento Portland es un conglomerante o cemento hidráulico que cuando se mezcla con áridos, agua y fibras de acero discontínuas y discretas tiene la propiedad de conformar una masa pétrea resistente y duradera denominada hormigón. Es el más usual en la construcción utilizado como aglomerante para la preparación del hormigón o concreto. Como cemento hidráulico tiene la propiedad de fraguar y endurecer en presencia de agua, al reaccionar químicamente con ella para formar un material de buenas propiedades aglutinantes.
Fue inventado en 1824 en Inglaterra por el constructor Joseph Aspdin. El nombre se debe a la semejanza en aspecto con las rocas que se encuentran en la isla de Pórtland, en el condado de Dorset. A diferencia de lo que muchos creen, su origen no está relacionado con Portland, Oregón, EEUU.
La extracción de estos minerales se hace en canteras, que preferiblemente deben estar próximas a la fábrica, con frecuencia los minerales ya tienen la composición deseada, sin embargo en algunos casos es necesario agregar arcilla, o calcáreo, o bien minerales de hierro, bauxita, u otros minerales residuales de fundiciones.
Esquema de un horno.La mezcla es calentada en un horno especial, con forma de un gran cilindro (llamado kiln) dispuesto casi horizontalmente, con ligera inclinación, que rota lentamente. La temperatura aumenta a lo largo del cilindro hasta llegar a unos 1400 °C, que hace que los minerales se combinen pero sin que se fundan o vitrifiquen.
En la zona de menor temperatura, el carbonato de calcio (calcáreo) se disocia en óxido de calcio y dióxido de carbono (CO2). En la zona de alta temperatura el óxido de calcio reacciona con los silicatos y forma silicatos de calcio (Ca2Si y Ca3Si). Se forma también una pequeña cantidad de aluminato tricálcico (Ca3Al) y ferroaluminato tetracálcico (Ca4AlFe). El material resultante es denominado clinker. El clinker puede ser conservado durante años antes de proceder a la producción del cemento, con la condición de que no entre en contacto con el agua.[1]
La energía necesaria para producir el clinker es de unos 1.700 julios por gramo, pero a causa de las pérdidas de calor el valor es considerablemente más elevado. Esto comporta una gran demanda de energía para la producción del cemento y, por tanto, la liberación de gran cantidad de dióxido de carbono en la atmósfera, un gas de efecto invernadero.
Para mejorar las características del producto final al clinker se agrega aproximadamente el 2% de yeso y la mezcla es molida finamente. El polvo obtenido es el cemento preparado para su uso.
El cemento obtenido tiene una composición del tipo:
64% óxido de calcio
21% óxido de silicio
5,5% óxido de aluminio
4,5% óxido de hierro
2,4% óxido de magnesio
1,6% sulfatos
1% otros materiales, entre los cuales principalmente agua.
Cuando el cemento Portland es mezclado con agua, se obtiene un producto de características plásticas con propiedades adherentes que solidifica en algunas horas después y endurece progresivamente durante un período de varias semanas hasta adquirir su resistencia característica. El endurecimiento inicial es producido por la reacción del agua, yeso y aluminato tricálcico, formando una estructura cristalina de calcio-aluminio-hidrato, estringita y monosulfato.
El sucesivo endurecimiento y el desarrollo de fuerzas internas de tensión derivan de la reacción más lenta del agua con el silicato tricálcico formando una estructura amorfa llamada calcio-silicato-hidrato. En ambos casos, las estructuras que se forman envuelven y fijan los granos de los materiales presentes en la mezcla. Una última reacción produce el gel de silicio (SiO2). Las tres reacciones generan calor.
Con el agregado de materiales particulares al cemento (calcáreo o cal) se obtiene el cemento plástico, que fragua más rápidamente y es más fácilmente trabajable. Este material es usado en particular para el revestimiento externo de edificios.
La calidad del cemento Portland deberá estar de acuerdo con la norma ASTM C 150.
En el 2004, los principales productores mundiales de cemento de Portland fueron Lafarge en Francia, Holcim en Suiza y Cemex en México. Algunos productores de cemento fueron multados por comportamiento monopólico.
[editar] Reacciones de formación del clinker
Las reacciones de la formación del clinker, por fases de temperatura, son:
de 1.000 a 1.100 °C
3CaO+Al2O3 → 3CaOAl2O3
2CaO+SiO2 → 2CaOSiO2
CaO+Fe2O3 → CaOFe2O3
de 1.100 a 1.200 °C
CaOFe2O3+3CaOAl2O3 → 4CaOAl2O3Fe2O3
de 1.250 a 1.480 °C
2CaOSiO2+CaO → 3CaOSiO2
La composición final será de:
51% 3CaOSiO2
26% 2CaOSiO
11% 3CaOAl2O3
12% 4CaOAl2O3Fe2O3
[editar] Reacciones de hidratación
Las reacciones de hidratación, que forman el proceso de fraguado son:
2(3CaOSiO2) + (x+3)H2O → 3CaO2SiO2xH2O + 3Ca(0H)2
2(2CaOSiO2)+ (x+1)H2O → 3CaO2SiO2xH2O + Ca(0H)2
2(3CaOAl2O3)+ (x+8)H2O → 4CaOAl2O3xH2O + 2CaOAl2O38H2O
3CaOAl2O3 + 12H2O + Ca(0H)2 → 4CaOAl2O313H2O
4CaOAl2O3Fe2O3 + 7H2O → 3CaOAl2O36H2O + CaOFe2O3H2O
Estas reacciones son todas exotérmicas. La más exotérmica es la hidratación de 3CaOAl2O3, seguida de la de 3CaOSiO2, y luego 4CaOAl2O3Fe2O3 y finalmente 2CaOSiO2.
Función del yeso
El yeso, o aljez, es generalmente agregado al clinker para regular el fraguado. Su presencia hace que el fraguado se concluya aproximadamente en 45 minutos. El yeso reacciona con el aluminato tricálcico para formar una sal expansiva llamada 'ettringita'.
3CaOAl2O3 + 3(CaSO42H2O) + 26H2O → 3CaOAl2O33CaSO432H2O
Cementos Portland especiales
Los cementos Portland especiales son los que se obtienen de la mismo modo que el cemento portland normal, pero tienen características diferentes a causa de variaciones en el porcentaje de los componentes que lo conforman.
Tipos de cementos Portland
Cemento Portland normal (CPN), o común, sin aditivos, es el más empleado en construcción.
Cemento Portland blanco (PB), compuesto por materias primas pobres en hierro, que le dan ese color blanquecino grisáceo. Se emplea para estucos, terrazos, etc.
Cemento Portland de bajo calor de hidratación (CBC), produce durante el fraguado una baja temperatura de hidratación; se obtiene mediante la alteración de los componentes químicos del cemento Portland común.
Cemento Portland de elevada resistencia inicial (CER), posee un mayor contenido de silicato tricálcico que le permite un fraguado más rápido y mayor resistencia. Se emplea en muros de contención y obras hidráulicas.
Cemento Portland resistente a los sulfatos (CPS), tiene bajo contenido en aluminato tricálcico, que le permite una mayor resistencia a la acción de sulfatos contenidos en el agua o en el terreno.
Cemento Portland con aire ocluido, tiene un aditivo especial que produce un efecto aireante en el material.
3.2 Etapas de la fabricación del cemento
-Explotación de materias primas: Consiste en la extracción de las piedras calizas y las arcillas de los depósitos o canteras, las cuales dependiendo de sus condiciones físicas se hacen los diferentes sistemas de explotación, luego el material se transporta a la fábrica. -Preparación y clasificación de las materias primas: Una vez extraídos los materiales, en la fábrica se reduce el tamaño de la caliza siguiendo ciertas especificaciones dada para la fabricación. Su tamaño se reduce con la trituración hasta que su tamaño oscile entre 5 a 10mm. -Homogenización: Consiste en hacer mezcla de las arcillas y calizas, que ya han sido trituradas, se lleva por medio de bandas transportadoras o molinos, con el objetivo de reducir su tamaño hasta el orden de diámetro de medio milímetro. En ésta etapa se establece la primera gran diferencia de los sistemas icade producción del cemento, (procesos húmedos y procesos secos). -Clinkerización: Consiste en llevar la mezcla homogeneizada a hornos rotatorios a grandes temperaturas aproximadamente a 1450°C, en la parte final del horno se produce la fusión de varios de los componentes y se forman gránulos de 1 a 3 cm de diámetro, conocido con el nombre de clinker. -Enfriamiento: Después que ocurre el proceso de clinkerización a altas temperaturas, viene el proceso de enfriamiento en la cual consiste en una disminución de la temperatura para poder trabajar con el material, éste enfriamiento se acelera con equipos especializados. -Adiciones finales y molienda: Una vez que el clinker se halla enfriado, se prosigue a obtener la finura del cemento, en la cual consiste en moler el clinker, después se le adiciona yeso con el fin de retardar el tiempo de fraguado. -Empaque y distribución: Esta última etapa consiste en empacar el cemento fabricado en bolsas de 50 kilo, teniendo mucho cuidado con diversos factores que puedan afectar la calidad del cemento, luego se transporta y se distribuye con cuidados especiales.
3.3 Clasificación de los cementos 3.3.1 Cementos naturales Conglomerantes hidráulicos que resultan de la calcinación de mezclas naturales caliza más arcilla, seguida de una fina molturación, por lo tanto podemos decir que son cales hidráulicas. Está contraindicado para hormigones resistentes y hormigón armado. 3.3.2 Cementos artificiales de portland Son todos aquellos cementos que su fabricación parte de mezclas de caliza más arcilla, hay una constancia de composición la cual no se da en la margas naturales.
3.4 Cualidades del cemento
-Resistencia: la resistencia a la comprensión, es afectada fuertemente por la relación agua/cemento y la edad o la magnitud de la hidratación. -Durabilidad y flexibilidad: ya que es un material que no sufre deformación alguna. -El cemento es hidráulico porque al mezclarse con agua, reacciona químicamente hasta endurecer. El cemento es capaz de endurecer en condiciones secas y húmedas e incluso, bajo el agua. -El cemento es notablemente moldeable: al entrar en contacto con el agua y los agregados, como la arena y la grava, el cemento es capaz de asumir cualquier forma tridimensional. -El cemento (y el concreto hecho con él) es tan durable como la piedra. A pesar de las condiciones climáticas, el cemento conserva la forma y el volumen, y su durabilidad se incrementa con el paso del tiempo. -El cemento es un adhesivo tan efectivo que una vez que fragua, es casi imposible romper su enlace con los materiales tales como el ladrillo, el acero, la grava y la roca. -Los edificios hechos con productos de cemento son más impermeables cuando la proporción de cemento es mayor a la de los materiales agregados. -El cemento ofrece un excelente aislante contra los ruidos cuando se calculan correctamente los espesores de pisos, paredes y techos de concreto.
Fue inventado en 1824 en Inglaterra por el constructor Joseph Aspdin. El nombre se debe a la semejanza en aspecto con las rocas que se encuentran en la isla de Pórtland, en el condado de Dorset. A diferencia de lo que muchos creen, su origen no está relacionado con Portland, Oregón, EEUU.
La extracción de estos minerales se hace en canteras, que preferiblemente deben estar próximas a la fábrica, con frecuencia los minerales ya tienen la composición deseada, sin embargo en algunos casos es necesario agregar arcilla, o calcáreo, o bien minerales de hierro, bauxita, u otros minerales residuales de fundiciones.
Esquema de un horno.La mezcla es calentada en un horno especial, con forma de un gran cilindro (llamado kiln) dispuesto casi horizontalmente, con ligera inclinación, que rota lentamente. La temperatura aumenta a lo largo del cilindro hasta llegar a unos 1400 °C, que hace que los minerales se combinen pero sin que se fundan o vitrifiquen.
En la zona de menor temperatura, el carbonato de calcio (calcáreo) se disocia en óxido de calcio y dióxido de carbono (CO2). En la zona de alta temperatura el óxido de calcio reacciona con los silicatos y forma silicatos de calcio (Ca2Si y Ca3Si). Se forma también una pequeña cantidad de aluminato tricálcico (Ca3Al) y ferroaluminato tetracálcico (Ca4AlFe). El material resultante es denominado clinker. El clinker puede ser conservado durante años antes de proceder a la producción del cemento, con la condición de que no entre en contacto con el agua.[1]
La energía necesaria para producir el clinker es de unos 1.700 julios por gramo, pero a causa de las pérdidas de calor el valor es considerablemente más elevado. Esto comporta una gran demanda de energía para la producción del cemento y, por tanto, la liberación de gran cantidad de dióxido de carbono en la atmósfera, un gas de efecto invernadero.
Para mejorar las características del producto final al clinker se agrega aproximadamente el 2% de yeso y la mezcla es molida finamente. El polvo obtenido es el cemento preparado para su uso.
El cemento obtenido tiene una composición del tipo:
64% óxido de calcio
21% óxido de silicio
5,5% óxido de aluminio
4,5% óxido de hierro
2,4% óxido de magnesio
1,6% sulfatos
1% otros materiales, entre los cuales principalmente agua.
Cuando el cemento Portland es mezclado con agua, se obtiene un producto de características plásticas con propiedades adherentes que solidifica en algunas horas después y endurece progresivamente durante un período de varias semanas hasta adquirir su resistencia característica. El endurecimiento inicial es producido por la reacción del agua, yeso y aluminato tricálcico, formando una estructura cristalina de calcio-aluminio-hidrato, estringita y monosulfato.
El sucesivo endurecimiento y el desarrollo de fuerzas internas de tensión derivan de la reacción más lenta del agua con el silicato tricálcico formando una estructura amorfa llamada calcio-silicato-hidrato. En ambos casos, las estructuras que se forman envuelven y fijan los granos de los materiales presentes en la mezcla. Una última reacción produce el gel de silicio (SiO2). Las tres reacciones generan calor.
Con el agregado de materiales particulares al cemento (calcáreo o cal) se obtiene el cemento plástico, que fragua más rápidamente y es más fácilmente trabajable. Este material es usado en particular para el revestimiento externo de edificios.
La calidad del cemento Portland deberá estar de acuerdo con la norma ASTM C 150.
En el 2004, los principales productores mundiales de cemento de Portland fueron Lafarge en Francia, Holcim en Suiza y Cemex en México. Algunos productores de cemento fueron multados por comportamiento monopólico.
[editar] Reacciones de formación del clinker
Las reacciones de la formación del clinker, por fases de temperatura, son:
de 1.000 a 1.100 °C
3CaO+Al2O3 → 3CaOAl2O3
2CaO+SiO2 → 2CaOSiO2
CaO+Fe2O3 → CaOFe2O3
de 1.100 a 1.200 °C
CaOFe2O3+3CaOAl2O3 → 4CaOAl2O3Fe2O3
de 1.250 a 1.480 °C
2CaOSiO2+CaO → 3CaOSiO2
La composición final será de:
51% 3CaOSiO2
26% 2CaOSiO
11% 3CaOAl2O3
12% 4CaOAl2O3Fe2O3
[editar] Reacciones de hidratación
Las reacciones de hidratación, que forman el proceso de fraguado son:
2(3CaOSiO2) + (x+3)H2O → 3CaO2SiO2xH2O + 3Ca(0H)2
2(2CaOSiO2)+ (x+1)H2O → 3CaO2SiO2xH2O + Ca(0H)2
2(3CaOAl2O3)+ (x+8)H2O → 4CaOAl2O3xH2O + 2CaOAl2O38H2O
3CaOAl2O3 + 12H2O + Ca(0H)2 → 4CaOAl2O313H2O
4CaOAl2O3Fe2O3 + 7H2O → 3CaOAl2O36H2O + CaOFe2O3H2O
Estas reacciones son todas exotérmicas. La más exotérmica es la hidratación de 3CaOAl2O3, seguida de la de 3CaOSiO2, y luego 4CaOAl2O3Fe2O3 y finalmente 2CaOSiO2.
Función del yeso
El yeso, o aljez, es generalmente agregado al clinker para regular el fraguado. Su presencia hace que el fraguado se concluya aproximadamente en 45 minutos. El yeso reacciona con el aluminato tricálcico para formar una sal expansiva llamada 'ettringita'.
3CaOAl2O3 + 3(CaSO42H2O) + 26H2O → 3CaOAl2O33CaSO432H2O
Cementos Portland especiales
Los cementos Portland especiales son los que se obtienen de la mismo modo que el cemento portland normal, pero tienen características diferentes a causa de variaciones en el porcentaje de los componentes que lo conforman.
Tipos de cementos Portland
Cemento Portland normal (CPN), o común, sin aditivos, es el más empleado en construcción.
Cemento Portland blanco (PB), compuesto por materias primas pobres en hierro, que le dan ese color blanquecino grisáceo. Se emplea para estucos, terrazos, etc.
Cemento Portland de bajo calor de hidratación (CBC), produce durante el fraguado una baja temperatura de hidratación; se obtiene mediante la alteración de los componentes químicos del cemento Portland común.
Cemento Portland de elevada resistencia inicial (CER), posee un mayor contenido de silicato tricálcico que le permite un fraguado más rápido y mayor resistencia. Se emplea en muros de contención y obras hidráulicas.
Cemento Portland resistente a los sulfatos (CPS), tiene bajo contenido en aluminato tricálcico, que le permite una mayor resistencia a la acción de sulfatos contenidos en el agua o en el terreno.
Cemento Portland con aire ocluido, tiene un aditivo especial que produce un efecto aireante en el material.
3.2 Etapas de la fabricación del cemento
-Explotación de materias primas: Consiste en la extracción de las piedras calizas y las arcillas de los depósitos o canteras, las cuales dependiendo de sus condiciones físicas se hacen los diferentes sistemas de explotación, luego el material se transporta a la fábrica. -Preparación y clasificación de las materias primas: Una vez extraídos los materiales, en la fábrica se reduce el tamaño de la caliza siguiendo ciertas especificaciones dada para la fabricación. Su tamaño se reduce con la trituración hasta que su tamaño oscile entre 5 a 10mm. -Homogenización: Consiste en hacer mezcla de las arcillas y calizas, que ya han sido trituradas, se lleva por medio de bandas transportadoras o molinos, con el objetivo de reducir su tamaño hasta el orden de diámetro de medio milímetro. En ésta etapa se establece la primera gran diferencia de los sistemas icade producción del cemento, (procesos húmedos y procesos secos). -Clinkerización: Consiste en llevar la mezcla homogeneizada a hornos rotatorios a grandes temperaturas aproximadamente a 1450°C, en la parte final del horno se produce la fusión de varios de los componentes y se forman gránulos de 1 a 3 cm de diámetro, conocido con el nombre de clinker. -Enfriamiento: Después que ocurre el proceso de clinkerización a altas temperaturas, viene el proceso de enfriamiento en la cual consiste en una disminución de la temperatura para poder trabajar con el material, éste enfriamiento se acelera con equipos especializados. -Adiciones finales y molienda: Una vez que el clinker se halla enfriado, se prosigue a obtener la finura del cemento, en la cual consiste en moler el clinker, después se le adiciona yeso con el fin de retardar el tiempo de fraguado. -Empaque y distribución: Esta última etapa consiste en empacar el cemento fabricado en bolsas de 50 kilo, teniendo mucho cuidado con diversos factores que puedan afectar la calidad del cemento, luego se transporta y se distribuye con cuidados especiales.
3.3 Clasificación de los cementos 3.3.1 Cementos naturales Conglomerantes hidráulicos que resultan de la calcinación de mezclas naturales caliza más arcilla, seguida de una fina molturación, por lo tanto podemos decir que son cales hidráulicas. Está contraindicado para hormigones resistentes y hormigón armado. 3.3.2 Cementos artificiales de portland Son todos aquellos cementos que su fabricación parte de mezclas de caliza más arcilla, hay una constancia de composición la cual no se da en la margas naturales.
3.4 Cualidades del cemento
-Resistencia: la resistencia a la comprensión, es afectada fuertemente por la relación agua/cemento y la edad o la magnitud de la hidratación. -Durabilidad y flexibilidad: ya que es un material que no sufre deformación alguna. -El cemento es hidráulico porque al mezclarse con agua, reacciona químicamente hasta endurecer. El cemento es capaz de endurecer en condiciones secas y húmedas e incluso, bajo el agua. -El cemento es notablemente moldeable: al entrar en contacto con el agua y los agregados, como la arena y la grava, el cemento es capaz de asumir cualquier forma tridimensional. -El cemento (y el concreto hecho con él) es tan durable como la piedra. A pesar de las condiciones climáticas, el cemento conserva la forma y el volumen, y su durabilidad se incrementa con el paso del tiempo. -El cemento es un adhesivo tan efectivo que una vez que fragua, es casi imposible romper su enlace con los materiales tales como el ladrillo, el acero, la grava y la roca. -Los edificios hechos con productos de cemento son más impermeables cuando la proporción de cemento es mayor a la de los materiales agregados. -El cemento ofrece un excelente aislante contra los ruidos cuando se calculan correctamente los espesores de pisos, paredes y techos de concreto.
viernes, 12 de agosto de 2011
Concreto
ESTRUCTURAS
Arquitecto: Rem Koolhaas (Oficina de Arquitectura Metropolitana)
Estructura: construcción de la CCTV, Beijing
Año Completo: Todavía en construcción
Número de votos: 3 (más 2 votos a favor de "la obra más significativa de la arquitectura creada hasta ahora en el siglo 21")
Por Nikolas Koenig / Trunkarchive.com.
Arquitecto: Rem Koolhaas (Oficina de Arquitectura Metropolitana)
Estructura: Biblioteca central de Seattle
Año Completo: 2004
Número de votos: 6 (más votos a 3 para "la obra más significativa de la arquitectura creada hasta ahora en el siglo 21")
Por Robert Polidori.
Suscribirse a:
Entradas (Atom)